AERODYNAMIC DESIGN AND CROSS -
COUNTRY FLIGHT PERFORMANCE ANALYSIS
OF DIANA - 2 SAILPLANES
Krzysztof Kubrynski
Tech_Soar_KK.pdf
A FLIGHT TEST EVALUATION OF
THE SZD 56-2 DIANA 2 RACING CLASS SAILPLANE
Richard H. Johnson
INTRODUCTION
The SZD 56-2 is a new 15-meter Racing Class sailplane that was evolved
from the previously tested SZD 56-1 Diana 1 15 meter wingspan flapped
sailplanes. This sailplane's competition performance history is
impressive. Sebastian Kawa won the 2005 Sailplanes Grand Prix Race in
France with it, Janusz Centka did likewise in the 15-meter class at
the 2006 World Championships in Sweden. The Diana 2 utilizes highly
reclining cockpit seating and a right cockpit side control
stick, as did the earlier Diana 1. The workmanship and detail design
of our test sailplane were outstandingly good. Its white lacquer
painted exterior surfaces were beautifully smoothed, polished, and
waxed. The wing area is only about 93 square feet, and its
aspect ratio measures about 26, which is very high for a 15-meter
sailplane. Its wing airfoils are reported to be a thin new highly
laminar KL-002-128F/17 design at the root, and a KL-002-122F/17 at the
tip. The wing is equipped with one-piece flaperons on each panel, and
each flaperon is equipped with 2 small NACA type ram-air inlets
designed to feed blow-hole turbulators located on the flaperons bottom
sides. This is excellent new light-weight carbon and aramide fiber
epoxy bonded composite sailplane.
Its
empty weight as delivered with 4 small (2.25 in diameter) basic
instruments was only 397 lbs. Adding radio, more instruments, and 2
batteries increased our flight test empty weight to about 420 lbs.
Most controls connected automatically during assembly, but the flaperons and elevator connected manually with reliable Polish hooks
that were secured by spring-loaded sleeves.
The Diana 2 has now been in
production for about 1.5 years and has a European Type Certificate for
the JAR-22 Utility Class (non-aerobatic). Our test sailplane was FAA
licensed as experimental, as are many US racing sailplanes.
We were fortunate in that Jerry
Zieba, the Diana dealer from Illinois, offered to bring his new Diana
2 to Caddo Mills for the Dallas Gliding Association�s flight-testing.
He kindly allowed Dean Carswell, Jeff Baird and me to use his
sailplane for flight-testing and evaluation. We made a detailed
inspection of this sailplane, and were impressed with both its
workmanship and very good quality. The wing surface waviness was very
low, averaging well below the .004inch limit that I believe to be
needed to achieve extensive low drag laminar flow on sailplane wings.
Its epoxy/carbon fiber composite construction appeared to be quite
strong, and its empty weight fully equipped with factory winglets,
instruments, and two batteries was unusually light at about 420 lbs.
That made it very easy to move about the hangar and airport.
The details of its construction
were all very well done. The exposed metal fittings were nicely
cadmium plated for enduring rust protection. Its retractable main
landing wheel is a relatively small 4.00 x 4-inch Tost unit that is
equipped with a standard drum brake, the same as with my Ventus A. The
difference is that the Diana�s landing wheel is well sprung with a
knuckle pivot joint and spring shock absorber system that nicely help
smooth the takeoffs and landings on rough surfaces.
A word of caution about the landing
gear extension and retraction system operation is warranted. It is a
good and well-designed system, but a bit different from most of the
other sailplanes I have flown. The cockpit actuation handle moves
forward for gear up, and aft for gear down, like many other
sailplanes, but there are no visible detents in the cockpit side floor
below the handle. Instead, the landing gear actuation handle is
equipped with a spring-loaded lever on its forward side that securely
locks the handle in either its gear full extended or gear fully
retracted positions. When retracting the landing gear, one must
squeeze the locking lever, to unlock it before the landing gear handle
can be moved forward to retract the wheel. Then one must release the
spring-loaded locking lever so that it can then catch its gear-up lock
detent when the gear handle is pushed fully forward. The reverse is
true when lowering the landing gear. The landing gear handle needs to
be moved aft rather swiftly to ensure that the down-lock engages its
detent properly. It is then prudent to check that the gear is locked
down properly by trying to move the gear handle forward without
squeezing lock actuation lever. If you can then move the gear handle
forward at all, the gear is not locked down. If so, then you need to
push the gear handle part way forward, and then slam it fully back,
while being careful that the spring-loaded locking lever is free to
find its locking detent.
The
aft end of the fuselage is equipped with a small 4-inch diameter solid
plastic tail wheel. It rattles a bit when landing and taking off, but
works OK. The towhook is installed on the fuselage bottom side about 2
feet aft of the nose. The towhook mechanism on our test sailplane did
not have an automatic back-release capability; therefore it was
placarded for aero towing only.
AIRSPEED CALIBRATION
The Diana 2 airspeed system uses a fuselage nose pitot tube that is
located in the cockpit ventilation air inlet. Small vent holes in the
fuselage nose sides serve as its static sources. First we checked the
pitot and static system lines for leaks, and found none. Then, while
inside the hangar and out of the wind, we calibrated the sailplane�s
Winter airspeed indicator by carefully comparing its readings to our
calibrated reference ASI meter. The errors that we measured for the
sailplane�s Winter ASI were relatively low, less than about 2 knots
over our entire planned flight test range. Those measured airspeed
indicator instrument error data are shown in Figure below.

I then made
our airspeed system flight calibration with two 11,000-foot high
tows. The sailplane was equipped with a trailing bomb static
reference, deployed in flight after tow release, and a Kiel tube
reference pitot temporarily taped to one side of the canopy. The
flight test calibration was then steadily flown at indicated airspeeds
of 35 to 120 kts, comparing our master reference indicated airspeeds
to those of the sailplane�s. The wing flap settings used were those
recommended by the sailplane�s Flight Handbook. They varied from +28
degrees at 35 kts to �2 degrees at 120 kts. Those test data were then
used to compute the Diana 2 airspeed system errors versus
indicated airspeed. The Figure below chart presents the flight
measured Airspeed System errors. There it is assumed that the
airspeed indicator has no errors. The Diana�s airspeed system measured
errors appear to be small, and generally about 1.5 kts or less over
the entire 40 to 120 kt IAS test range. In general, our test data
measurements show that the Diana 2 is actually flying about one knot
faster than the indicated airspeed, which is very good.

While the fuselage nose side static
pressure orifices provide a good static pressure source, they are
subject to clogging when flying in rain. For that reason a pneumatic
switch of some kind should be installed, and teed into the sailplane�s
static pressure line so that the pilot can switch to an alternate
static source if and when clogging occurs within the basic static
pressure line. Venting the alternate static pressure source to the
cockpit usually provides a relatively good static reference pressure,
and I have used that a number of times in the past.
SINK RATE TEST
FLIGHTS
For these
tests we had to wait until the atmosphere became relatively calm with
little vertical air motion or horizontal wind shear at the flight test
altitudes. It had been a windy and dry fall season in Texas, but
finally on the 7th of November the atmosphere became
acceptably calm for a few days of flight-testing. Six high tow test
flights were performed to measure the Diana 2 sink rates at various
airspeeds. The wing flap settings used were those recommended by the
sailplane�s Flight Handbook. They varied from +28 degrees at 35 kts,
to �2 degrees at 120 kts indicated airspeed. A total of 96 sink rate
measurements were made, two by Jeff Baird and 4 by me. Of those 96
sink rate data points, only 4 needed to be discarded because of their
excessive scatter.
The
remaining 92 sink rate test data points from these 6 flights were then
averaged at each test airspeed. They were then corrected to the sea
level 59 deg F standard atmosphere air conditions, and then shown
plotted in Figures below. A
minimum sink rate of only about 100 fpm is indicated at 35 to 40 kts.
Figure below shows the corresponding L/D data points. There a
remarkable L/D of about 47:1 at 51 kts are indicated.
This is the highest
L/Dmax we have ever measured for a 15-meter sailplanes!
Subsequent
thermal soaring tests showed that the Diana 2 climbed very well in our
weak Texas November thermals. The above-discussed performances were
measured with the water ballast tanks dry. We did not test with the
ballast tanks filled. Had we done so, we would have likely achieved
another 1 or 2 L/D points because of the lowered skin friction drag
coefficients that result from flying at higher airspeeds.
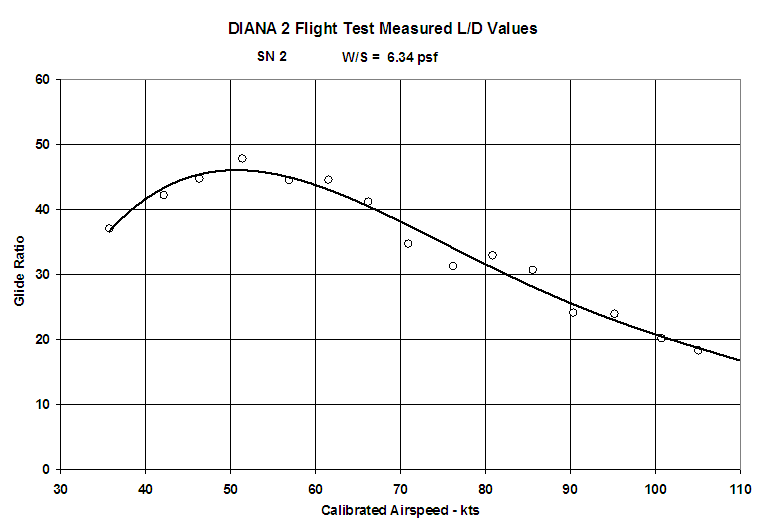

WING OIL FLOW TESTS
The
factory had installed full span turbulator blow-holes on the flaperon
bottom surfaces, located well aft at about the wing .95 chord
location. Wing oil flow test flights were not conducted because of
concern that the very small blow-holes might become clogged by the
oil.
WING SURFACE WAVINESS MEASUREMENTS
Using
our standard 2-inch long wave gage, we made chordwise waviness
measurements of our test Diana 2�s wing top and bottom surfaces at 14
spanwise stations along each wing panel,. The magnitudes of the
Diana�s wing surface waves were amazingly small, averaging only about
.0012 inches peak-to-peak. That is extremely smooth. Only at
the wing panel roots, and again near the wing tip top surfaces, did
our measurements much exceed that value. Those waviness measurements
are for peak-to-peak magnitudes �from valleys to peaks. Those data are
shown plotted in Figure below.

GENERAL CHARACTERISTICS
The Diana 2�s airbrakes and water
ballast dump controls connect automatically upon assembly. The
elevator and flaperon controls must be connected manually, but that is
not difficult to accomplish because their connections are easily
accessible and simple to connect. The cockpit is enclosed by a long
forward hinged canopy that extends from behind the pilot�s head to
forward of the rudder pedals. I noted that if I wore white shoes while
flying, they reflected badly onto the canopy at times; therefore it is
better to wear dark colored shoes while flying the Diana. The
plexiglas canopy itself has very good optics, except for a minor
distortion at its very front end. The cockpit forward and sideward
visibility are excellent, thanks mainly to the low cockpit side rails
and the wing flaps that allow the Diana to avoid flying in a nose-up
attitude at low airspeeds.
The cockpit fitted me well, but
larger pilots will likely find it a bit snug. When flying the Diana,
the pilot needs to rest in a more-reclined body position than I am
used to, but not as much so as the older Swiss Diamont sailplane
cockpits required. In any case, the well-reclined pilot�s body
position was comfortable, but it took a while to get used to. The
cockpit seatback is ground-adjustable, and the rudder pedals and
headrest are adjustable in-flight. My 155 lb weight and 70 inch
height needed the seatback to be positioned near its aft limit when
wearing a parachute, but the rudder pedals were set nearer to their
mid-position. Tall pilots will likely need to remove the seatback
entirely. I have been happily flying my Ventus A that way for years.
The Diana 2
is easy to fly, and it handles well. Its stall characteristics are
surprisingly gentle, with almost no tendency for the sailplane to drop
a wing during my low airspeed maneuvering tests. My 45-to-45 degree
roll rate measurement test showed about 4 seconds at 50 kts, but I am
not sure that I had the control stick fully deflected. I
found the side-stick aileron
control forces are a little higher than my Ventus A at thermalling
speeds. They increased considerably at high airspeeds; but maybe that
is a good feature to help prevent pilots from over-stressing the wings
at high airspeeds.
The wing root
spar arrangement is unusual in that both the left and right hand spar
stubs are permanently attached to the fuselage. The wing panel roots
have sockets that fit onto the fuselage mounted spar stubs. The oval
shaped monocoque fiberglass trailer is strong but light in weight with
a low slung and attractive appearance. The ends of the wings are
cradle mounted, and their trailer forward-end cradles roll on rail
guides. When removing or stowing the wings, one needs to only enter
slightly into the rear entrance of the trailer. The fuselage is stowed
on a wheeled dolly that also serves as the fuselage support when
assembling or disassembling the sailplane.
Each wing panel weighs about 100
lbs, and is equipped with 2 large integral water ballast tanks. One
water tank is located in the forward portion of the wing panel, and
one is located in the aft portion. Their combined total capacity is
listed as 65.5 US gallons, or 547 lbs. Also, a 1.5-gallon tail fin
tank is provided to optimize the flight CG, when and if needed. To
fill the wing tanks, a unique fiberglass dual funnel is provided that
connects to both the forward and aft tank wing bottom surface outlet
valves simultaneously. This loading funnel assembly rests securely on
the wing upper surface, and commendably no hands are needed to
stabilize it when loading water ballast. A single rubber stopper is
provided in the dual outlet funnel, such that the pilot can choose to
load water into either the forward or aft tank separately; or leaving
the stopper free, both tanks are loaded simultaneously.
The Diana�s airbrakes are
Schempp-Hirth type double plated wing top surface only units. They
perform quite well in flight. However, care must be taken to not open
them abruptly at high airspeeds. As with most sailplanes equipped with
powerful top surface only airbrakes, their rapid extension above about
70 kts causes a strong reduction in wing lift. That is sometimes
sufficient to put the pilot�s head through the canopy if he is not
tightly strapped in. Sailplanes equipped with both wing top and bottom
surface airbrakes are much more benign in that respect, in that they
do not appear to exhibit any significant delta �G� effects when the
airbrakes are extended suddenly at high airspeeds.
The early winter thermals that
existed during our Caddo Mills flight-testing were weak, but we were
able to easily soar it at the end of some of our test data runs.
During that limited weak thermal testing, I thought that it thermalled
well, and its 100 fpm minimum sink rate served me well.
Dean Carswell performed the
sailplane�s flying qualities testing. He was able to also evaluate the
Diana�s thermalling flight characteristics, and he will present his
evaluations separately.
The current price of the new Diana
2 is EU 64,000, plus trailer, instruments and shipping. The
instruments, water ballast filling funnels, seat-back, and other
auxiliary items are currently not included in the sailplane�s basic
price. The beautiful light-weight fiberglass trailer adds 11,950 EU to
the price, and that includes all of the needed trailer support
fittings and cradles, and the clever fuselage support jack fixture.
For more options contact Jerry at
[email protected],
and/or look at
www.dianasailplanes.com.
for additional pricing and details.
SUMMARY
The new Diana 2
sailplane is, in my opinion, an excellent new sailplane for
competition and racing. Its light empty weight makes it easy to
assemble and handle on the ground. It appears to be of high quality in
design, construction, and finish. Its powerful Schempp-Hirth type
airbrakes are easy to operate and provide very good landing approach
control.
Many thanks go to Jerry Zieba for bringing his fine new sailplane 950
miles from Illinois for our flight tests in Texas, and to the Dallas
Gliding Association for providing both the hangarage and the high aero
tows needed to accomplish it. Also to Southwest Soaring�s manager,
Leslie Hamm and her Caddo Mills tow pilots, David Cheek and Howard
Hughes, who did the excellent towing. They usually required only about
18 minutes to tow The Diana to 12,000 ft AGL with the powerful Pawnee.
REFERENCES
A.
Johnson, R.H., A
Flight Test Evaluation Of The Diana Racing Sailplane; Soaring-
April 1999
_____________________________________________________________________________________________________
DIANA 2
Sport pilot report
By Bill Liscomb
�Whoever designed this will never be accused of copying anybody or
anything,� proclaimed fellow glider pilot Bob Backer, visiting while
the Diana 2 was being readied for its� first flight. That is what
attracted me to the Diana 2 � it is a total departure from
convention. Decades of designing/building/flying both R/C gliders and
hang gliders helped me to appreciate the unique design concepts
applied to this little racer. I like stuff that is different.
I picked
it up in Galveston,
TX in the middle of June, saving about $1000. in
shipping costs and two weeks in time. Got it home, filled the panel,
got the paperwork done and flew it
June 31, 2006. As
of this writing, I have 28 flights and about 100 hours in it. Here�s
the story.
Trailer/Assembly/Disassembly. The trailer is as different as the
glider. The fuselage has spar stubs sticking out each side, so the
trailer is wider than normal to accommodate it. The wings are hung
from dollies above the fuselage. The fuselage is held in a dolly with
the gear up. The dolly is designed for smooth paving of some sort,
and doesn�t work so well in the sandy soil at
Warner
Springs.
I made a �rolling kickstand� to slide on one spar stub, so now the
dolly can stay in the trailer. The fuselage is pushed about 30 feet
aft of the trailer, then the wings are pulled out and put on. The
Diana 2 sits low to the ground, and the wingtips are about hip level,
and the helper on the tip doesn�t have much weight to bear. The wings
are light, and the root feels lighter than some tips I�ve helped
with. Each wing has one pin, and once the wings are on, the
horizontal stabilizer and its cover, the TE probe and the winglets are
put on. The flaperons and elevator are manual connect with very
positive locking connectors. Now that I have a system to
assemble/disassemble, it is actually pretty easy and quick. It isn�t
better or worse than anything else, just totally different�
Before I
bought it, my main concern was, �Can I fit in it?� It is a tiny
little thing! The first time I pulled out the fuselage, I thought it
was an 80% scaled R/C model. But, at 5� 10� and 175lbs I do fit
comfortably in it with my chute. The critical dimension is from your
tailbone to the top of your head. If you have short legs and are my
height, you may not fit. This is an all out racer with no extra
anything, including room. However, I�ve done a 6 hour 45 minute
flight and was very comfortable. I�ve flown side stick before and the
only problem with side stick is thinking about it before you fly.
Once in the air - no problem. The pilot position is more reclined
than anything else I�ve flown, and it did take a short while to get
used to flying so reclined. The pilot manual doesn�t call for
negative flaps for takeoff, but I�ve found that does really help. The
rudder has a pretty high aspect ratio, and is not very effective while
the tail is on the ground. Once the tail comes up, all is well. Add
positive flaps and a view of the towplane fills the canopy and it is
airborne.
Off tow
the fun really begins! It is easy to fly and the roll rate is
downright snappy. As with most flapped ships, as the flaps go farther
down, the adverse yaw goes up. But at normal climb/cruise settings it
is not noticeable and control harmony is good. I haven�t flown with
other ships very much, so I can�t claim any kind of remarkable
thermalling performance. I do know this thing has climbed out of
situations that my previous glider, a 304CZ, would have succumbed to.
The flying weight of the Diana 2 (without water ballast) is about 25
pounds heavier than the empty weight of the 304CZ! Empty weight of my
Diana 2 with instruments, battery, oxygen, etc., is 433lbs
Then
there is the glide. Unreal! I�m still having trust issues with the
glide computer. It seems impossible that a 15m ship has legs like
this! A nice sheet of linear graphs showing flap settings for speeds
at different wing loading is provided. The idea with the flap charts
is you cut them out and stack them together with a glue stick. As you
dump water, simply peel off charts until you get to your current wing
loading. The correct flap setting is mandatory to get the best
performance from this ship. In March of 2007, I did get to see what
a load of bugs does. I checked out my black, fuzzy leading edges,
then set the glide computer to 20% bugs and did a 30 mile final
glide. I got back to Warner very high, dialed the bugs back to zero,
and it showed my actual arrival altitude...
I�ve
done one flight with water ballast. I filled the front tanks in the
wings � 43gallons/344lbs plus another 12lbs in the tail, put me at
just under 1,000lbs (1102lbs max) and got the wing loading up to
10.6lbs sq ft. (dry it is about 6.7lbs sq ft) Once off tow, it
transformed into a rocket. I felt like I was strapped inside a
runaway locomotive. August 29th, 2006 was a great day in SoCal, and SeeYou showed two segments
over 170 miles with no turns and average speeds 113 and 116mph.
Landings
are easy. I use the +21 flap setting rather than the +28 because of
the wind we usually have at Warner Springs and also to keep the
ailerons more effective while dealing with the normal crosswind shear,
thermals and turbulence on final. Wheel landings are the norm � touch
down, add full spoilers, put flaps full negative, hold the tail off,
roll to stop.
The
Diana 2 is small and light, in the air and on the ground, and a total
blast to fly. Flying in Southern California is unique in that a pilot
can encounter several different air masses in one flight. Without
water ballast, the Diana 2 is very capable of handling these
conditions. It does very well in small, weak thermals as well as the
big rowdy stuff, and has an amazing glide over a wide speed range.
When it gets good, simply add water. Lots and lots of water�
Bill Liscomb
2BL
__________________________________________________________________________________________________
Janusz Centka
1000 km triangular !
December 10, 2002 FAI
ratified Janusz Centka World Speed Record over a triangular course
of 1000 km: 144.95
km/h
Janusz has flown SZD 56.1 -
Diana, N256DS, "ZJ"
His short story.
The forecast looked good
for July 30, 2002, so early that morning I got ready for my 1000 km
flight. Kempton Izunu, the weather guru in Nevada, suggested a
triangular task with the first turn at Jackpot, 300 km north of Ely.
But, because of the smoke from many forest fires in California, I
chose a new second turnpoint, 300 km west of Ely.I launched at 11:15 AM,
and made a perfect start at 11:30. My first thermal, a 9-knotter, took
me to 15000 feet MSL. The early thermals on course were mostly 8
knots, but as fast-moving cirrus arrived from the west, the thermals
gradually weakened, forcing me to fly left, and then right, of course.
At one point, I had to deviate 15 miles off-course, where I finally
found a 5-knotter and climbed to 12000 feet MSL above the first
turnpoint.On the second leg, the
weather improved, and I was able to fly cloud streets in 15 to 20 mile
segments without circling. After about 60 miles, the cirrus again made
its presence felt. Inter-thermal distances increased as good lift
became progressively harder to find, and I had to make do with 5 and
6-knot lift. Then Cu Cong began to form nearby, along with scattered
showers. Finally, with 60 miles to go to the second turn, things
suddenly looked much better. I found a 10-knot thermal and climbed
quickly to 17000 feet MSL. With good cu�s ahead, I reached the second
turnpoint a full hour ahead of schedule. On the last leg, I flew too far north,
and missed a nice cloud street south of course. I was forced to fly
through rain under the dissipating Cu Cong. Luckily, I found lift on
the edge of light rain, and was able to make my final glide. Having
finished ahead of schedule, I considered flying a longer task, using a
third turnpoint. But the terrain around Ely had quit working, so I
landed. It was a magnificent flight for me, and flying Diana was a big
pleasure . It is a great glider.
I
had the good fortune to pilot the first new production Diana at
the Uvalde 15 Meter Nationals and would like to offer a recount
of my impressions of this aircraft and how it performed against
the best pilots and sailplanes in the United States.
 Mr.
Jerry Zieba of Diana Sailplanes contacted me in April and kindly
offered Diana "Zulu Juliet" for me to fly in the 15M Nationals at
Uvalde. This aircraft would be the second production model Diana,
but the first aircraft produced by the newly formed Bogumil Beres
facility. The aircraft was finally shipped from Gdansk on 4 July.
Jerry picked it up in New York harbor on July 23. After a whirlwind
of driving and paperwork, Jerry miraculously arrived with the Diana
at Texas Soaring Association on July 29th.
With
no time for preparation and practice, I arrived in Uvalde on 1 August,
and conducted four practice flights prior to the competition. These
flights culminated with a winning speed of just under 100 mph on
the second practice day. My initial impressions of the Diana were
quite positive!
As
most people know, the trailer and assembly procedures are a bit
unusual in that the spar stubs are fixed to the fuselage instead
of to each wing. Substantial carbon fiber spar stubs protrude about
30" beyond either side of the fuselage. On assembly, the fuselage
is first rolled out of the trailer on a dolly which, by means of
a clever hydraulic jack, keeps the fuselage spar stubs above the
trailing edge of the wings. Upon removal of the fuselage from the
trailer, the ship is lowered until the main wheel is just on the
ground. The wings are then extracted from the trailer keeping the
leading edge of each wing above the fuselage spar as they are rolled
out. Some care is required to ensure that the wings are held sufficiently
high to avoid banging the spar stubs. However, this unusual practice
readily became routine and was aided by the extreme light weight
of the wing panels (approx 100 lbs ea.). As mentioned by "OC", handling
of the wing root is a challenge for the beginner in that there is
no spar stub to hang onto. Certainly, either technique or some type
of handling aid would take care of this. Overall, assembly is straightforward
and is aided by the light weight of the components.

The
quality of the components, fit and finish was at least equal to
the very best of the German ships. I ran my 2" wave gage over the
wings and could not find any noticeable sign of waviness. "Optically",
the wings were near perfect. However, the trailing edge of the left
spoiler did not seat perfectly. This condition seemed to disappear
in flight. The all-carbon construction gives the ship a very solid
and robust feel throughout.
The cockpit is
well laid out with the side stick on the right and all other controls
accessible by the left hand. There was never a need to "shift" hands
in flight as with some gliders. Actuation of the full span flaperon
was smooth as silk throughout the flap range. I "really" liked the
side stick. Actuation was smooth in both axis and seemed to cause
less fatigue on extended flights than a standard stick. However,
the Diana's ultrahigh roll rate does demand a relatively smooth
and precise technique.
The cockpit is
significantly more reclined than the typical racing class ship.
However, I would not describe it as "cramped". Leg room is a limiting
factor for pilots in excess of 6' in height. However, shoulder,
hip and elbow room were all much more generous than my Discus A.
The in-flight adjustable headrest was a nice feature. However,
another inch or so of leg room would be nice for taller pilots. As
mentioned on the NG, I did fly most of the contest barefoot. This
did provide a little extra leg room, but more significantly, my
white tennis were causing very distracting reflections. A good pair
of darker colored deck shoes would have solved this problem without
compromising leg room. Ventilation is good with a high volume
demister in the nose as well as an "aimable" vent located on the
cockpit sidewall near the control stick. I did note that the nose
vent, if left in the full open position, becomes unacceptably loud
over about 80 kts. However, when the flow is "throttled back", for
higher speeds, it provides adequate ventilation and is very quiet.
Visibility in
the Diana is outstanding. With the reclined seating, forward and
upward visibility is excellent. Behind, you can see the horizontal
and up front, a quick rock of the wings easily reveals any hazardous
traffic which may be ahead and directly below.
In
flight the Diana is very pleasant. I have never flown a glider with
such low adverse yaw characteristics. Full rate (ie. 3 seconds - 45
to 45) rolls into thermals can be done with only 2/3 rudder. The
resulting maneuverability provides a competitive advantage in
centering and rolling in and out of thermals. The Diana offers the
option to roll 90 degrees into a turn, change your mind and roll
back onto course without delay or significant penalty. ZJ" was recognizable to other pilots from some
distance simply by the extremely agile manner in which the glider
maneuvered.
Performance:
Based on my experience in Uvalde, the Diana was equal to the best
of ASW-27's and V2's throughout the envelope. The ship did seem
particularly good in the important 90 to 110 knot range. On one
particular 55 mile, 110 knot, dead heat final glide, the Diana beat
a heavy '27 home by a comfortable margin. The Diana is limited to
10.3 PSF, which was perhaps a small disadvantage in Uvalde. Another
pound or so would have been nice under some of those incredible
cloudstreets.
Thermalling
is a joy because of the maneuverability, visibility and turn radius.
48 to about 53 knots seemed to be about right at gross weight. In
the larger gaggles, I could sometimes core the thermal in a much
smaller diameter and outclimb many of the ships. I never once had
the sense that any other ship, including the V2, had any advantage
in climb. I often ended up on the top of the weak pre-start gaggles
supporting my opinion that the ship would be excellent in light
conditions.
The
contest stats show that I was within a few tenths of 1% of the winner's
score on the AST days, but was about 5% off the mark on the PST's.
My continuing PST brain disconnects dropped my overall ranking on
the final day from 3rd to a still respectable 5th. Certainly, the
Diana can drag race with the best of them! Thanks again to Jerry
Zieba for entrusting me with his beautiful sailplane!
David Mockler aka Discus Driver "2XX"
|